As most of us here know, Nintex Process Manager is a process management tool designed to create and manage business processes with a focus on simplicity and collaboration. While it’s known for its process documentation, management, and improvement capabilities, it does not directly have a specific feature for value stream mapping. I receive many questions on this topic, so I wanted to lay out my thoughts. Value stream mapping is a lean-management method for analyzing the current state and designing a future state for the events that take a product or service from its beginning to the customer, focusing on reducing waste in the value chain.
However, Process Manager supports most aspects of value stream mapping through its process mapping, lean, and process improvement capabilities. It allows organizations to document processes, identify inefficiencies, and improve workflows, which are the key components of value stream mapping.
Implementing Value Stream Mapping in Nintex Process Manager: A Fictitious Example
Company: OrangeTech Innovations
OrangeTech Innovations is a fictional company specializing in eco-friendly technology solutions. The company aims to streamline its product development process to reduce waste and improve customer delivery time.
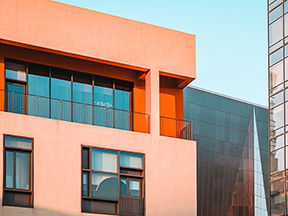
Value Chain Description
An example value chain at OrangeTech Innovations for their product, the SolarPanel Max, involves the following key steps:
- Conceptualization: Generating ideas based on market research and sustainability trends.
- Design: Creating detailed designs and prototypes of the SolarPanel Max.
- Sourcing: Procuring high-quality, eco-friendly materials.
- Manufacturing: Assembling the SolarPanel Max using sustainable practices.
- Quality Assurance: Ensuring the product meets strict sustainability and performance standards.
- Distribution: Delivering the product to retailers and customers efficiently.
- Customer Support: Offering robust support to ensure customer satisfaction and gather feedback for future improvements.
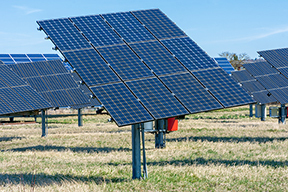
Modeling in Process Manager
To model this value chain in Nintex Process Manager, OrangeTech Innovations could take the following steps:
- Process Identification: First, identify and define all the processes in the value chain described above. This involves breaking down each key step into sub-processes. For example, the Manufacturing step could be broken down into sub-processes like Assembly, Testing, and Packaging.
- Process Mapping: Use Process Manager to create detailed process maps for each sub-process. This involves documenting each task, the responsible parties, the inputs and outputs, and the resources required. Attach relevant documents, videos, or links to each process for easy access.
- Waste Identification: As part of the mapping exercise, identify areas of waste or inefficiency within each process. This could include unnecessary steps, delays in handoffs, or overuse of resources.
- Collaboration and Feedback: Leverage Process Manager’s collaboration features to gather feedback from stakeholders involved in each process. This helps identify pain points and opportunities for improvement from those directly involved in the work.
- Improvement and Optimization: Modify the processes to eliminate waste and improve efficiency based on the feedback and identification of waste. This could involve redefining tasks, changing the sequence of operations, or introducing new tools to improve productivity.
- Continuous Improvement: Regularly review and update the process maps in Process Manager to reflect changes and improvements. Encourage ongoing feedback and use version control and change management features to keep everyone aligned.
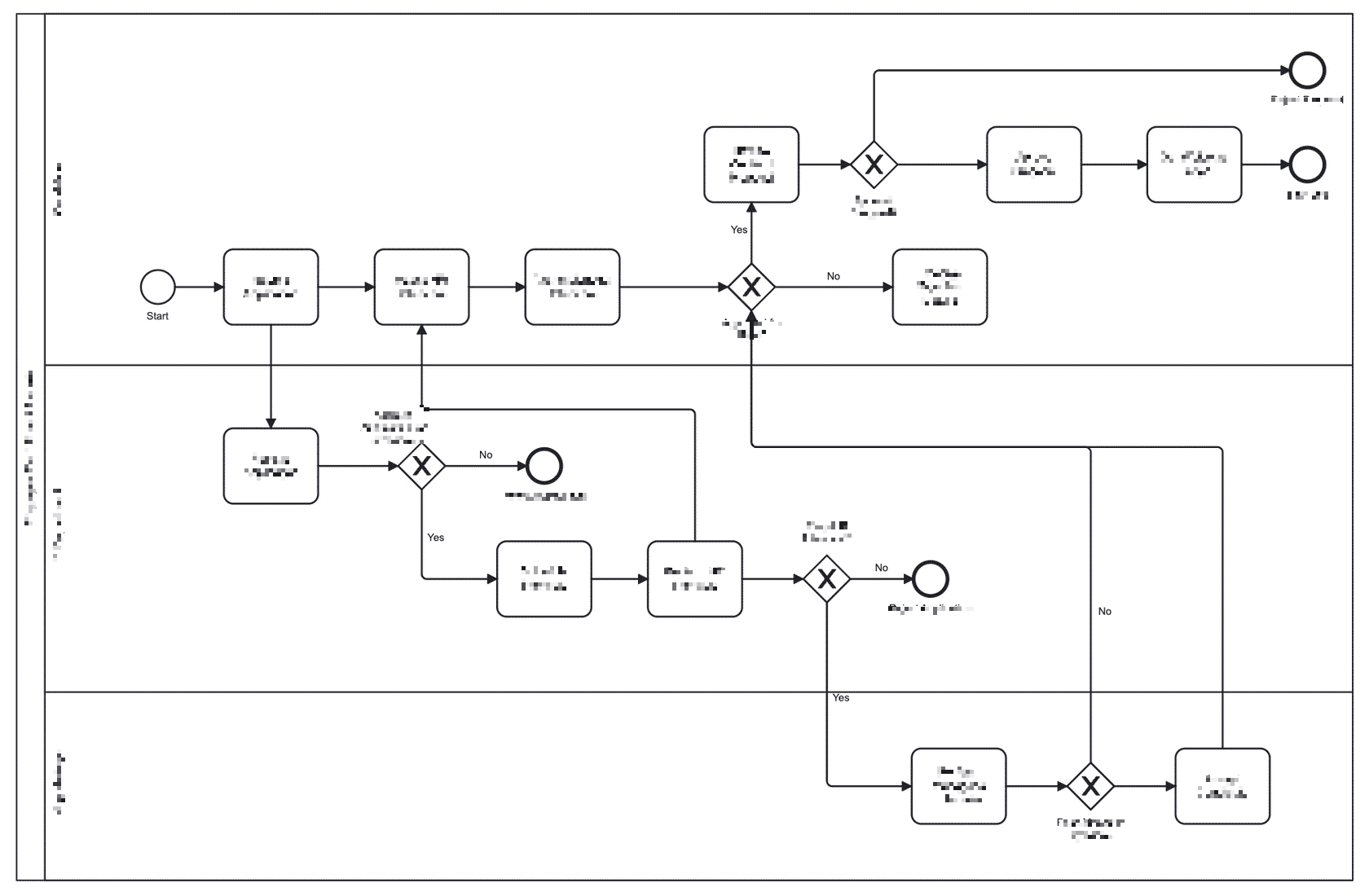
In this way, OrangeTech Innovations can effectively use Process Manager to support their value stream mapping efforts by focusing on process efficiency, waste reduction, and continuous improvement in alignment with lean management principles.
I’d love to hear your thoughts and experiences on this.